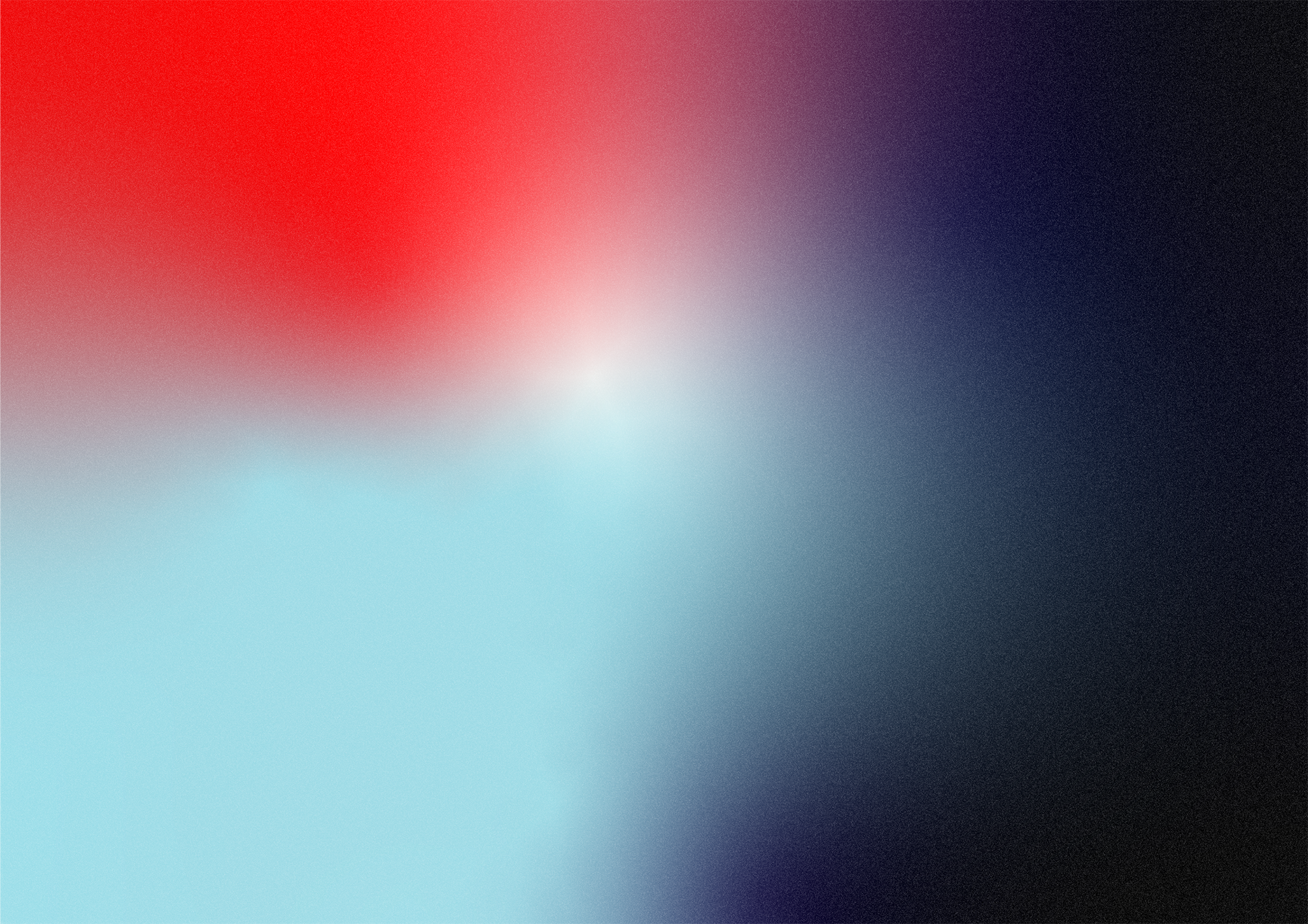
Helme exists to improve service line management in the mining industry by creating a more efficient and sustainable model for service line routing and maintenance.
Their product, the Damper Clamp™ - a ‘shock-absorber for service lines’ - introduces a patented clamp design, specifically engineered to limit cable wear and premature failures at clamping points and speed up installation and maintenance processes.
Helme is proudly female-founded and majority owned, and retains 100% of their design and manufacturing capability in Western Australia.
The Damper Clamp™: Achieve faster service line routing, with better results.
Mining companies are increasingly focused on lowering operating costs, reducing risk, improving reliability, and increasing productivity. Helme is interested in adding value across these metrics by introducing a more sustainable and effective model for the way service lines are installed, managed, and maintained. As a company, Helme is committed to delivering customer-driven innovation, via a socially responsible business model.
Critical service lines (electrical cables, hydraulic hoses, pneumatic lines etc.), are the veins and arteries of any mobile equipment or fixed plant machinery used in mining. When a service line fails, equipment goes down, resulting in lost productivity and revenue. In Australia, mechanical wear at clamping points is a prominent cause of service line failures on machinery. This wear is caused by poor vibration isolation and the physical and material design of existing clamping systems. Specifically, service line failures are responsible for up to 10% of downtime events on heavy mining equipment, and result in $200 - $300k of unnecessary cost (associated with parts, labour, and downtime) per machine, per year.
The physical design of existing clamping products (namely P-Clamps and cable ties) also hampers the efficiency, quality and reliability of service line installation, replacement and/or removal processes. This contributes to higher costs across parts (due to poor installation practices, failures occur), and labour (products are awkward and time-consuming to install).
In response to these issues, Helme has developed the Damper Clamp™. Made from robust, elastomeric material the Damper Clamp™ can absorb the vibrations that exist on mobile equipment and fixed plant machinery, protecting service lines from damage and contributing to longer periods of sustained uptime. The clamp also expedites the installation, replacement, and/or removal of service lines, and reduces parts and labor costs.
A key differentiator for the Damper Clamp™ is the separation of the mounting hole and the clamp's closing mechanism, allowing the clamp to be installed prior to service line routing and stay in place during service line maintenance and replacement activities. This is the main feature contributing to faster installation and maintenance processes (compared to the P-Clamp).
Another unique feature is the flexible cradle where the service line sits, which prevents service lines from being pinched and crushed due to over-tensioning of cable ties (reducing wear and failures). Helme’s patented leg design complements the flexible cradle in that it helps the clamp to move with and absorb vibrations and shocks as they occur.
Finally, thanks to its flexible material fewer sizes of Damper Clamp™ (compared to P-Clamps) are required to route lines between 6mm and 50mm, limiting the likelihood of service line damage caused by incorrect part selection / use.
The Damper Clamp™ can benefit almost every player in the mining industry, including original equipment manufacturers (OEMs), machine owners, contractors, and service providers. Clamps are used prolifically in mining and purchased as a commodity item.
As an example of the potential in this market, there are approximately 14,000 heavy mobile equipment (HME) in service in Australia at present. With an average of 350 clamps per machine, at an average price of ~$4/unit, the value of clamps on board HME in Australia alone is approximately AUD$20M. Extrapolated, the investment across the lifetime of the machines in the Australian HME market comes close to AUD$50M. Globally, the total addressable market for clamps, again just for HME, is in excess of AUD$270M. This does not account for clamps installed on fixed plant machinery or other equipment including rail.
Helme exists to enable customers to execute their service line routing and maintenance practices faster, more predictably, and with better results.
With its innovative Damper Clamp™ product, Helme aims to improve the efficiency of service line maintenance and management while reducing costs and downtime for the mining industry and those who service it.
As the company develops, it will explore the relevance of the Damper Clamp™ to other industries and geographies.